Recovering Waste Heat from Slags: Reuse of Energy
- Justin Chen
- Jan 14, 2024
- 6 min read
6 Methods of utilizing metallurgical slags to combat climate change and promote sustainability

According to the International Energy Agency (IEA), industries worldwide generate a significant amount of waste heat: around 67% of the energy that is used, is wasted. This figure is estimated to be around 400 Exajoules (EJ) annually. This amount of energy could power the United States for 3 years!. One area that often goes unnoticed in the quest for sustainable solutions is the recovery of waste heat from metallurgical slags during steel-making. In this blog post, we will delve into the significance of this technology and explore its potential to contribute to climate change mitigation and sustainability efforts.
Are Metallurgical Slags The Heat?
They are physically THE HEAT...
The steel-making industry produces 1.8 billion tons of steel per year. It contributes to 8% of global energy demand and about 10% of CO2 emissions, globally. This makes it an incredibly large industry that has the capability to reduce emissions if the right technology was implemented to increase efficiency.
Metallurgical slags, a byproduct of metal smelting processes, are typically considered waste materials with little value. Often, they are passively cooled and sent to landfills for disposal. However, they possess a property that we really shouldn't consider as waste - waste heat.
In steel-making, slags are produced during the separation of the molten steel from impurities in steel-making furnaces.
Figure 1. The composition of impurities in pig iron (in percentages)
You see, iron ore combines with carbon dioxide makes steel. However, in order to make the highest quality steel, impurities must be removed from the iron. To do this, oxygen gas is pumped into the melted iron ore mixture. The oxygen reacts with the impurities, forming solid materials that can be separated from the molten iron. These solid materials have extremely high thermal energy because they reach temperatures above 3,000 degrees fahrenheit or 1700 degrees celsius. Waste heat refers to the thermal energy that is released as a byproduct during various industrial processes. In the case of metallurgical slags, substantial amounts of waste heat are generated during the cooling and solidification of molten metals. For every ton of steel made, 25 Gigajoules (GJ) of energy are used and 15 GJ are released as waste heat in the form of slags.
15 GJ: could theoretically power a lightbulb for roughly 2 million years! The world produces 1.8 billion tons of steel per year.
27 Billion GJ: Is the total steel-making waste energy per year. Again, a wild statistic, but with that energy, you could power a lightbulb for 36 quadrillion years, with WASTE HEAT from steel-making alone! :)

Extracting Value from Waste Heat:
Recovering waste heat from metallurgical slags presents an opportunity to harness this energy for productive use. Researchers have been exploring innovative techniques to capture and utilize this heat efficiently.
1. Sensible Heat Recovery:
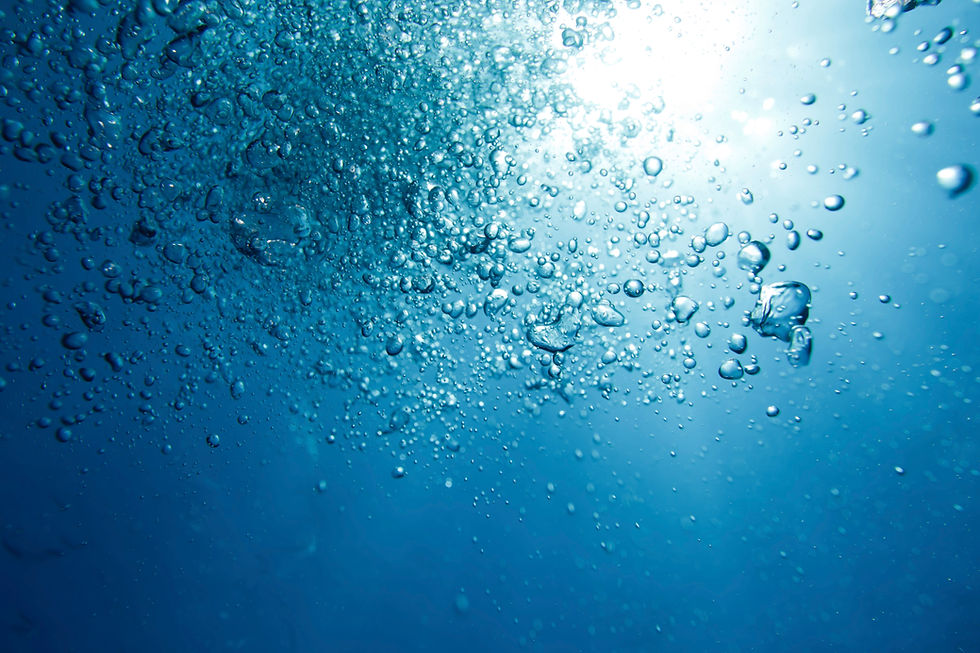
Sensible heat recovery is a straightforward method that capitalizes on the temperature difference between the hot slag and the environment. Slags, with temperatures reaching thousands of degrees Celsius, are in contact with cooler surroundings during the steelmaking process (for example: water). To recover sensible heat, researchers employ heat exchangers with high thermal conductivity. These heat exchangers transfer the heat from the hot slag to a fluid, such as water, without undergoing any phase change. As the fluid absorbs the heat, its temperature rises, and it is then channeled into a heat recovery system. One of the best techniques to heat water, creating steam, to generate electricity in a steam turbine. There are other applications, including preheating combustion air or supplying district heating networks directly to homes.The key challenge in this method lies in designing efficient heat exchangers capable of handling the harsh conditions of the slag environment while maximizing the heat transfer rate for optimal energy recovery.
2. Latent Heat Recovery:
Latent heat recovery involves capturing the energy released during phase changes of certain slags. Slags may undergo solidification or crystallization, releasing latent heat during the process. To harness this energy, researchers study the phase transition behavior of slags and identify the specific temperature ranges at which latent heat is released. By carefully controlling the cooling process, it is possible to ensure that slags experience phase changes, thereby releasing latent heat. Heat exchangers or cooling systems are then employed to capture and transfer this latent heat to a working fluid like water. The energy-rich fluid can then be utilized for electricity generation or other heat-intensive industrial processes. Successful implementation of latent heat recovery demands a deep understanding of the slag's thermodynamic properties and precise control over the cooling rates to ensure optimal energy extraction.
3. Thermochemical Processes:
Thermochemical processes involve chemical reactions to recover waste heat from slags. Researchers explore different chemical reactants that can effectively extract heat from the slags. The process typically starts with mixing the slags with a suitable chemical substance, resulting in an exothermic reaction that releases heat. This liberated heat can then be used for steam generation, powering turbines for electricity production, or for other industrial heat requirements. Developing efficient chemical reactions and finding the right reactants that can be easily regenerated for repeated use are some of the challenges in this method. Additionally, ensuring that the reaction products do not cause environmental or operational issues is crucial for the success of thermochemical heat recovery systems.
4. Magnetic Induction:
Magnetic induction is a cutting-edge method that exploits the principles of electromagnetic induction to recover waste heat from slags. In this process, the slags are subjected to alternating magnetic fields generated by specialized equipment. As the magnetic fields change rapidly, eddy currents are induced within the slags, resulting in localized heating due to electrical resistance. This localized heating causes the slags to release their waste heat, which can then be captured and utilized for various purposes. Researchers focus on optimizing the design of the magnetic induction systems to achieve efficient heat transfer while ensuring safety and minimizing energy losses. Additionally, the magnetic properties of the slags themselves play a crucial role in determining the effectiveness of this method, making material research and selection an essential aspect of developing a successful waste heat recovery system.
5. Thermoelectric Conversion:
Thermoelectric conversion is a fascinating method that directly converts heat sources into electrical power using thermoelectric materials. When exposed to a temperature gradient, these materials generate an electric current, enabling the conversion of waste heat from slags into usable electricity. To implement this method, researchers embed thermoelectric devices within the slag-containing systems. As the slags release heat, the thermoelectric modules harvest the temperature difference to produce electricity. The key challenge in this approach is to identify and optimize thermoelectric materials with high conversion efficiency and stability under the harsh operating conditions of steel plants. Ongoing research in material science and thermoelectric engineering is critical for further advancing this method.
6. Coupling with Cogeneration Systems:
Coupling waste heat recovery from slags with cogeneration systems combines multiple approaches to maximize energy efficiency. In this method, the recovered waste heat is simultaneously utilized for electricity generation and heating applications. The recovered heat can power steam turbines or gas turbines to produce electricity, while also providing heat for industrial processes or district heating networks. Researchers focus on developing integrated systems that efficiently channel the waste heat to both electricity generation and heating components, minimizing energy losses and maximizing overall plant efficiency. This approach offers a comprehensive solution to reduce greenhouse gas emissions and enhance energy sustainability in the steel industry.
Significance:

The importance of recovering waste heat from slags becomes even more evident when considering its potential impact on climate change. Steel-making is one of the leading CO2 producers in the world. The heat needed for the steel-making process requires a lot of carbon dioxide emissions from fossil fuels, and so any slag heat that is wasted contributes substantially to its energy efficiency. The integration of waste heat recovery technology in industries can significantly reduce their overall energy consumption, consequently lowering greenhouse gas emissions. This approach aligns perfectly with the broader goal of achieving a low-carbon economy and combating the adverse effects of global warming.
Conclusion:
The recovery of waste heat from metallurgical slags is an ingenious solution that represents the power of technology in shaping a more sustainable world. By focusing on cutting-edge research and innovative applications, we can unlock the full potential of waste heat recovery and its crucial role in combatting climate change. As we move towards a greener and more sustainable future, it is crucial to recognize the importance of technologies like waste heat recovery from slags. By converting what was once considered waste into a valuable resource, we take a significant step towards minimizing our environmental impact and mitigating climate change. As researchers continue to refine and expand this technology, its potential to revolutionize industries and contribute to global sustainability efforts becomes ever more apparent.
Author's Note:
In this rapidly evolving world, every step we take towards sustainability matters. Waste heat recovery from metallurgical slags exemplifies the transformative power of technology in addressing climate change and promoting a more environmentally conscious society. As we continue to explore groundbreaking solutions, I am optimistic about the positive impact these innovations will have on our shared future.
Works Cited
Barati, M., & Jahanshahi, S. (2020). Granulation and heat recovery from metallurgical slags. Journal of Sustainable Metallurgy, 6(2), 191–206. https://doi.org/10.1007/s40831-019-00256-4
Sun, Y., Zhang, Z., Liu, L., & Wang, X. (2015). Heat recovery from high temperature slags: A review of chemical methods. Energies, 8(3), 1917–1935. https://doi.org/10.3390/en8031917
Zhang, H., Wang, H., Zhu, X., Qiu, Y.-J., Li, K., Chen, R., & Liao, Q. (2013). A review of waste heat recovery technologies towards molten slag in steel industry. Applied Energy, 112, 956–966. https://doi.org/10.1016/j.apenergy.2013.02.019
Comments